Die Cast Mold Makers: Crafting Excellence in Metal Fabrication
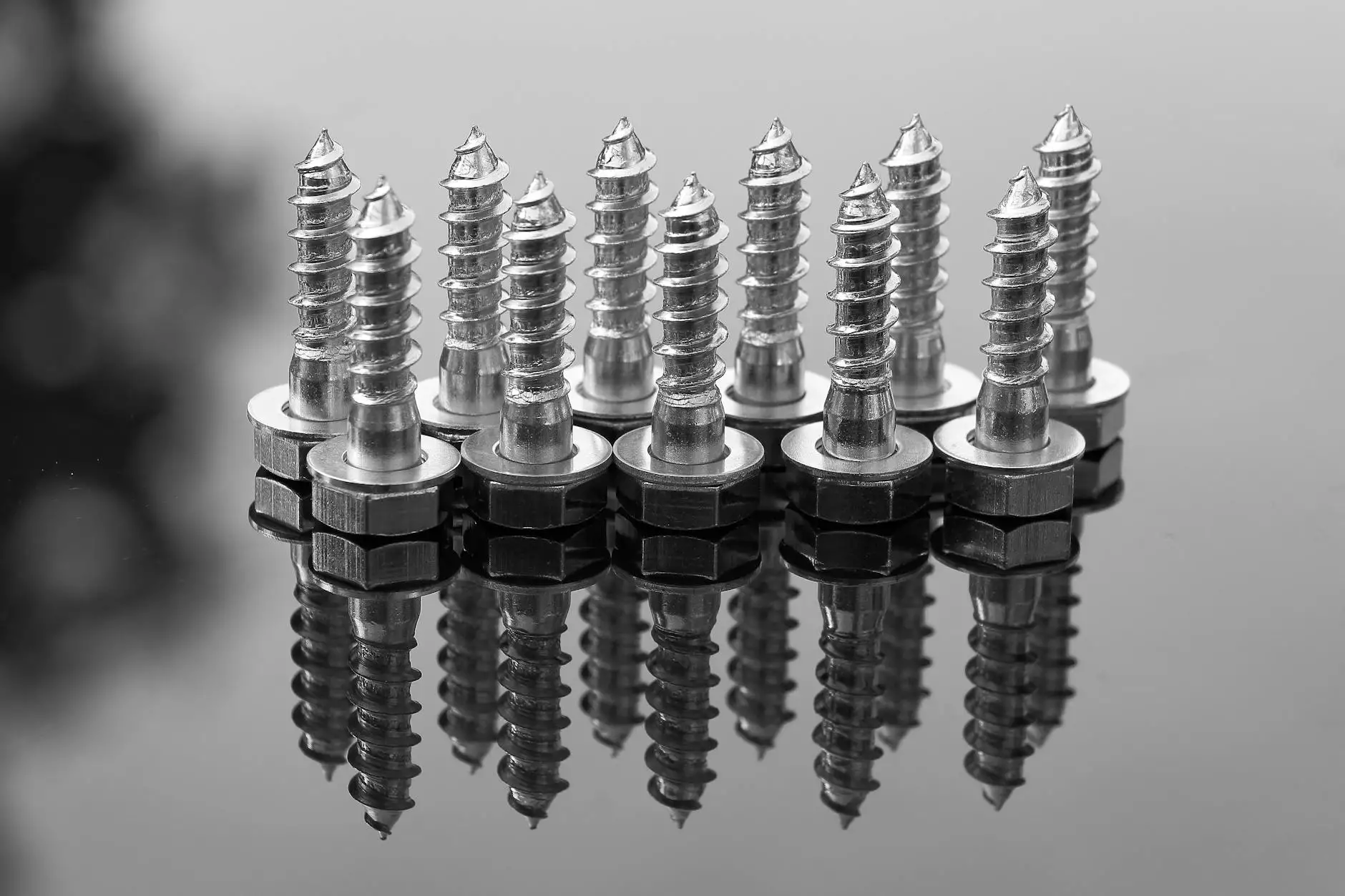
The manufacturing industry thrives on precision, innovation, and the relentless pursuit of quality. Die cast mold makers sit at the heart of this endeavor, transforming metal into intricate shapes and designs that are essential for various sectors, including automotive, aerospace, and consumer products. This article delves into the vital role of die cast mold makers, their techniques, innovations, and the overall impact they have on the metal fabrication industry.
The Art and Science of Die Casting
Die casting is a highly efficient metal fabrication technique that allows for the mass production of parts with excellent dimensional accuracy and surface finish. The process involves forcing molten metal under high pressure into a mold cavity. This approach not only minimizes waste but also enhances the mechanical properties of the final products. The skills of die cast mold makers are crucial in designing and creating the molds used in this process.
Understanding the Die Casting Process
Die casting can be categorized primarily into two types: hot chamber die casting and cold chamber die casting. Each method has its specific applications and advantages:
- Hot Chamber Die Casting: This method is suitable for metals with low melting points, such as zinc and magnesium. The molten metal is injected into the mold using a hydraulic system. It is characterized by faster cycle times and efficiency.
- Cold Chamber Die Casting: Best suited for metals with higher melting points, such as aluminum and copper. In this method, the molten metal is poured into a chamber before being injected into the mold. This allows for better control over the casting process.
Key Advantages of Die Casting
The popularity of die casting stems from its numerous benefits, which include:
- High Precision: Die casting produces parts with high dimensional accuracy, which is crucial for assembly in complex systems.
- Excellent Surface Finish: The molds can create parts with a smooth surface, reducing the need for secondary finishing operations.
- Complex Shapes: The dies can be designed to produce intricate shapes that are often difficult to achieve with other methods.
- Material Efficiency: Minimal waste is generated, making it an eco-friendly option for metal manufacturing.
- Scalability: Once the die is created, parts can be produced in large quantities, making it cost-effective for mass production.
The Role of Die Cast Mold Makers
Die cast mold makers are specialists in designing and constructing the molds used in the die casting process. Their expertise is critical in determining the quality and success of the final product. The following components highlight the multifaceted role of mold makers in this industry:
Designing the Mold
The first step in the die casting process begins with mold design. Mold makers utilize advanced CAD (Computer-Aided Design) software to create detailed designs that meet the specifications of the desired part. Important factors considered during the design phase include:
- Part Geometry: The shape of the part influences the mold design. Complex geometries require precise calculations to ensure effective flow of molten metal.
- Draft Angles: Appropriate draft angles are incorporated to facilitate the removal of the cast part from the mold without damage.
- Cooling Channels: Efficient cooling is essential for optimizing cycle times and achieving uniform cooling rates throughout the mold.
- Ventilation: Proper venting prevents trapped air from creating defects in the cast part.
Manufacturing the Mold
Once the design is finalized, mold makers proceed with the manufacturing process. This involves several key steps:
- Material Selection: High-quality steel is selected for the mold construction to withstand the high pressures and temperatures during the casting process.
- Machining: Advanced CNC (Computer Numerical Control) machines are employed to precisely fabricate the mold components.
- Assembly: The individual components are assembled into a functioning mold, ensuring proper alignment and fit.
- Testing: Prototypes are often produced to test the mold's performance, ensuring that it meets all specifications before full production.
Innovations in Die Casting Technology
The die casting industry is continuously evolving, driven by technological advancements and the demand for higher efficiency and lower costs. Recently, several innovations have emerged that significantly impact the role of die cast mold makers:
3D Printing and Rapid Prototyping
3D printing technology has revolutionized the way mold makers develop and test molds. With the ability to quickly produce prototypes, Mold makers can test designs and make adjustments before committing to expensive machining processes. This reduces lead times and increases the customization capabilities of die cast molds.
Advanced Materials and Coatings
The development of new materials and coatings for molds has enhanced their durability and performance. For instance:
- Metal Matrix Composites: These materials offer superior strength and wear resistance, leading to longer-lasting molds.
- Surface Treatments: Coatings such as nitriding or hard anodizing improve the mold's resistance to wear and corrosion.
Automation in Metal Fabrication
Automation technology has streamlined the die casting process by integrating robotics into operations. Automated systems enhance precision, reduce labor costs, and improve safety by minimizing human intervention in hazardous environments.
Challenges Faced by Die Cast Mold Makers
Despite the advancements in technology, die cast mold makers encounter several challenges in their operations, including:
Cost of Materials
The rising costs of quality materials can strain budgets, especially for smaller mold-making companies. Mold makers must continuously seek cost-effective material options while maintaining high standards.
Maintaining Precision
As the complexity of designs increases, achieving and maintaining precision becomes a challenge. Mold makers need to stay updated with the latest machining technologies to continue delivering high-quality molds.
Competition and Market Pressure
The die casting market is highly competitive, with constant pressure to reduce lead times and pricing while maintaining high-quality standards. Companies that fail to adapt to market demands risk losing clientele to more agile competitors.
Future of Die Casting and Mold Making
The future of die casting, particularly regarding mold making, is bright. With continued technological innovation and a growing emphasis on sustainability, the industry is poised for significant growth. Key trends to watch include:
- Increased Use of Recycled Metals: As sustainability becomes a priority, the use of recycled materials in die casting will likely increase.
- Enhanced Data Analytics: Companies are expected to leverage data analytics to improve the die casting process continuously.
- Collaboration Across Industries: Partnerships between die casting companies and other sectors will foster innovation and create new opportunities.
Conclusion: The Integral Role of Die Cast Mold Makers in Manufacturing
In conclusion, die cast mold makers play an essential role in the realm of metal fabrication. Their expertise in designing and manufacturing high-quality molds is crucial for producing intricate parts that meet the ever-growing demands of various industries. While challenges remain, the future of die casting is full of potential, driven by innovation, sustainability, and a dedicated workforce passionate about excellence. As we move forward, the contributions of die cast mold makers will undoubtedly shape the future of manufacturing, making it a vibrant and impactful field.